The Powerhouse of Modern Manufacturing – A Complete Guide for Global Buyers
Explore the technology, applications, and benefits of injection motors. Learn how high-efficiency injection motors optimize industrial processes, reduce energy costs, and drive sustainability.
Introduction
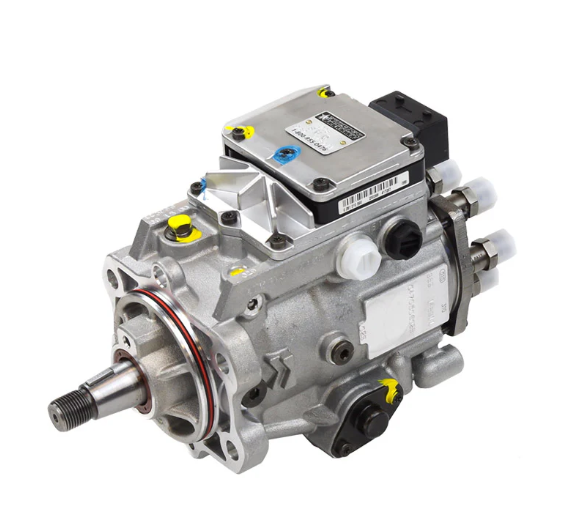
As industries worldwide strive for precision, energy efficiency, and sustainability, injection motors have become indispensable in powering critical machinery like plastic injection molding systems, automotive manufacturing lines, and packaging equipment. With over [X] years of expertise in motor manufacturing and global trade, we understand the pivotal role these motors play in maintaining competitive advantage.
This 4,000-word guide delves into the engineering brilliance of injection motors, their applications across sectors, and how to select the right motor for your needs. Designed for procurement managers, engineers, and business leaders, this resource combines technical depth with actionable insights to help you optimize operations and reduce total cost of ownership.
1. What Is an Injection Motor?
An injection motor is a specialized electric motor designed to deliver high torque, precise speed control, and reliability in demanding industrial processes, particularly in injection molding machines. These motors convert electrical energy into mechanical power to drive screws, pumps, and hydraulic systems that shape raw materials (e.g., plastics, metals) into finished products.
Key Components of Injection Motors:
- Stator and Rotor: Core elements generating electromagnetic force.
- Cooling System: Prevents overheating during continuous operation (e.g., liquid cooling or integrated fans).
- Encoder or Sensor: Ensures precise positioning and speed feedback.
- Drive Controller: Regulates power input for variable speed and torque demands.
Types of Injection Motors:
- Servo Injection Motors:
- Use permanent magnet technology for energy savings up to 80% compared to traditional motors.
- Ideal for high-precision tasks like medical device manufacturing.
- Hydraulic Injection Motors:
- Paired with hydraulic pumps for heavy-duty applications (e.g., automotive parts).
- All-Electric Injection Motors:
- Eliminate hydraulic systems, reducing energy waste and maintenance.
2. Why Injection Motors Are Critical for Industrial Success
2.1 Unmatched Energy Efficiency
- Servo-driven motors adjust power consumption in real-time, slashing energy use by 40–60% in injection molding cycles.
- Example: A [Case Study] showed a German automotive supplier reduced annual energy costs by €120,000 after switching to IE4-class injection motors.
2.2 Precision and Repeatability
- Achieve micron-level accuracy in product dimensions, crucial for industries like electronics and aerospace.
- Closed-loop control systems maintain ±0.1% speed stability, even under variable loads.
2.3 Durability in Harsh Conditions
- Built to withstand high temperatures (up to 155°C), dust, and chemical exposure.
- IP66-rated housings protect against water and particulate ingress in humid environments.
2.4 Reduced Downtime and Maintenance
- Brushless designs and self-lubricating bearings extend service intervals to 20,000+ hours.
- Predictive maintenance integration via IoT sensors cuts unplanned downtime by 30%.
2.5 Sustainability Compliance
- Meet global standards like EU Ecodesign 2025 and ISO 50001, aligning with corporate ESG goals.
3. Applications of Injection Motors Across Industries
3.1 Plastic Injection Molding
- Automotive: Produce dashboards, bumpers, and interior components with consistent quality.
- Consumer Goods: Manufacture toys, household items, and packaging materials at high speeds.
3.2 Metal Die-Casting
- Power hydraulic systems to inject molten aluminum or zinc into molds for engine parts and hardware.
3.3 Food and Pharmaceutical Packaging
- Servo motors ensure sterile, high-speed filling and sealing of bottles, blister packs, and syringes.
3.4 Renewable Energy
- Drive wind turbine blade molding machines and solar panel frame extrusion systems.
3.5 Robotics and Automation
- Integrated into robotic arms for precise handling of delicate components in electronics assembly.
4. How to Choose the Right Injection Motor
4.1 Assess Operational Requirements
- Load Profile: Cyclic vs. continuous duty (e.g., short bursts for molding vs. 24/7 operation).
- Torque and Speed: Calculate peak torque needs during injection phases (e.g., 500–5,000 Nm).
4.2 Prioritize Energy Efficiency
- Opt for IE4 or IE5 premium efficiency motors to qualify for government rebates and reduce lifecycle costs.
- Compare servo vs. hydraulic systems: Servo motors save 30–50% energy but have higher upfront costs.
4.3 Environmental and Safety Factors
- Explosion-Proof Motors: Required for hazardous areas (ATEX/IECEx certifications).
- Noise Levels: Select motors with noise emissions below 75 dB for indoor facilities.
4.4 Customization Options
- Mounting Configurations: Flange, foot, or face mounting for space-constrained setups.
- Shaft Modifications: Keyed, hollow, or splined shafts to match existing machinery.
4.5 Supplier Credentials
- Verify certifications like ISO 9001, CE, and UL.
- Choose suppliers offering 24/7 global support and spare parts availability.
5. Maintenance Best Practices for Longevity
5.1 Routine Inspections
- Weekly: Check for vibration anomalies and lubricant levels.
- Monthly: Clean cooling vents and test insulation resistance.
5.2 Common Failures and Solutions
- Bearing Wear: Replace bearings every 10,000 hours; use high-temperature grease.
- Overheating: Install thermal sensors and ensure ambient temperatures stay below 40°C.
5.3 Upgrade Opportunities
- Retrofitting older hydraulic systems with all-electric motors can cut energy use by 60%.
- Integrate smart controllers for real-time monitoring via Industry 4.0 platforms.
6. The Future of Injection Motor Technology
6.1 AI-Driven Optimization
- Machine learning algorithms predict motor performance degradation, enabling proactive repairs.
6.2 Lightweight Materials
- Carbon fiber-reinforced rotors and housings reduce weight by 25% without sacrificing durability.
6.3 Green Manufacturing
- Recyclable Motors: Designs using 90% recyclable materials to meet circular economy mandates.
- Hydrogen-Powered Motors: Pilot projects in 2024 aim to replace fossil-fuel-dependent systems.
6.4 5G Connectivity
- Ultra-low latency communication between motors and central controllers enhances synchronization in smart factories.
7. Why Partner with Us for Your Injection Motor Needs?
As a leading global exporter, we deliver:
- Cutting-Edge Technology: Patented servo motor designs with 98% efficiency.
- End-to-End Solutions: From motor selection to installation support.
- Cost Efficiency: Competitive pricing with bulk order discounts and DDP shipping terms.
- Sustainability Leadership: Motors compliant with 2025 EU RoHS 3 updates.
- Global Reach: Warehouses in the EU, North America, and Asia ensure fast delivery.
Conclusion
Injection motors are the unsung heroes of modern manufacturing, driving efficiency, precision, and sustainability across industries. By understanding their capabilities and partnering with a trusted supplier, businesses can achieve significant cost savings and operational resilience.
Explore our certified injection motor range today and discover how our expertise can power your next breakthrough.
Keywords: Injection motor, injection molding machine motor, high-efficiency industrial motors, servo injection motors, global motor suppliers.