The Ultimate Guide to Permanent Magnet Electric Motors: Efficiency, Applications, and Future Trends
Introduction
In an era where energy efficiency and sustainability dominate industrial innovation, permanent magnet electric motors (PM motors) have emerged as a cornerstone of modern engineering. As a leading manufacturer in the motor industry, we recognize the growing demand for high-performance, eco-friendly solutions. This comprehensive guide explores the technology behind PM motors, their advantages over traditional motors, diverse applications, and future trends—positioning your business to make informed decisions in a competitive market.
1. What Are Permanent Magnet Electric Motors?
Permanent magnet electric motors utilize powerful magnets (e.g., neodymium, samarium-cobalt) embedded in the rotor to generate a constant magnetic field. Unlike induction motors, which rely on electromagnets and slip mechanisms, PM motors eliminate energy loss from rotor currents, achieving higher efficiency and precision.
Key Components:
- Stator: Houses windings that create a rotating magnetic field.
- Rotor: Contains permanent magnets aligned to interact with the stator’s field.
- Control System: Advanced inverters regulate speed and torque with minimal energy waste.
Types of PM Motors:
- Brushless DC Motors (BLDC): Ideal for applications requiring variable speeds and low maintenance (e.g., drones, HVAC systems).
- Permanent Magnet Synchronous Motors (PMSM): Used in high-precision industrial machinery and electric vehicles (EVs).
2. Advantages of Permanent Magnet Motors
2.1 Unmatched Energy Efficiency
PM motors operate at 90–97% efficiency, outperforming induction motors (typically 75–85%). By eliminating rotor copper losses, they reduce energy consumption by up to 40% in industrial settings, translating to significant cost savings.
2.2 Compact Design and High Power Density
The strong magnetic fields enable smaller, lighter motors without sacrificing power. This makes PM motors ideal for space-constrained applications like robotics and EVs.
2.3 Low Maintenance and Longevity
With no brushes or slip rings (in BLDC models), PM motors experience less wear, reducing downtime and maintenance costs. Their robust construction ensures a lifespan exceeding 20,000 operational hours.
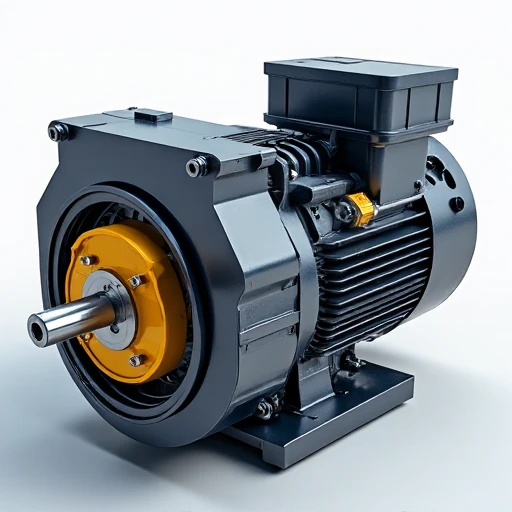
2.4 Precision Control
Integrated with smart inverters, PM motors deliver precise torque and speed control, critical for automation, CNC machines, and renewable energy systems.
3. Applications Across Industries
3.1 Industrial Automation
- Pumps and Compressors: PM motors optimize water treatment plants and HVAC systems, cutting energy use by 30%.
- Conveyor Systems: High torque at low speeds enhances material handling efficiency.
3.2 Electric Vehicles (EVs)
PM motors dominate EV drivetrains due to their lightweight design and regenerative braking capabilities. Leading automakers like Tesla and Toyota rely on PMSMs for extended battery range and acceleration.
3.3 Renewable Energy
- Wind Turbines: Direct-drive PM generators eliminate gearboxes, improving reliability in offshore wind farms.
- Solar Tracking Systems: BLDC motors adjust panel angles to maximize energy capture.
3.4 Consumer Electronics
From refrigerators to drones, PM motors enable quieter, energy-efficient operation.
4. How to Choose the Right PM Motor
4.1 Assess Load Requirements
- Constant vs. Variable Loads: PMSMs excel in dynamic applications; BLDC suits steady loads.
- Torque-Speed Curve: Match motor characteristics to operational demands.
4.2 Environmental Factors
- Temperature: Neodymium magnets may demagnetize above 150°C; consider samarium-cobalt for high-heat environments.
- Dust and Moisture: IP-rated housings protect motors in harsh conditions.
4.3 Cost vs. Performance Balance
While PM motors have higher upfront costs than induction motors, their energy savings often justify the investment within 1–2 years.
5. The Future of PM Motor Technology
5.1 Rare-Earth Material Innovations
Researchers are developing low-cost, high-strength magnets using cerium and lanthanum to reduce reliance on scarce neodymium.
5.2 Integration with IoT and AI
Smart motors embedded with sensors enable predictive maintenance, real-time performance monitoring, and seamless integration into Industry 4.0 ecosystems.
5.3 Sustainability Initiatives
Recycling programs for end-of-life magnets and eco-friendly manufacturing processes align with global circular economy goals.
Conclusion
Permanent magnet electric motors represent a transformative shift toward energy-efficient, sustainable industrial solutions. Their versatility across industries—from EVs to renewable energy—underscores their role in driving the green revolution.
As a trusted partner in motor manufacturing, we invite you to explore our tailored PM motor solutions designed to elevate your operational efficiency and reduce carbon footprints. Contact us today to discover how our cutting-edge technology can power your next project.