Discover how industries from manufacturing to healthcare choose the right geared motors. Learn key criteria, case studies, and future-ready strategies.
Introduction
The choice of a geared motor (reduction motor) can make or break operational efficiency, safety, and profitability in industrial applications. With advancements in automation, IoT, and sustainability regulations, selecting the right motor-gearbox combination requires a deep understanding of industry-specific demands. This guide breaks down the critical selection criteria for 8 major sectors, supported by real-world examples and data-driven insights for 2025.
1. Manufacturing & Automation
Key Requirements: Precision, high torque density, 24/7 reliability.
Selection Criteria:
- Motor Type: Brushless DC (BLDC) or servo motors with planetary gears for robotic arms (backlash <1 arcmin).
- Gear Design:
- Planetary Gears: For CNC machines requiring compact size and 200+ Nm torque.
- Helical Gears: Conveyor systems needing smooth operation (noise <65 dB).
- Case Study: A German automotive plant reduced welding robot downtime by 40% using IP67-rated planetary gear motors with integrated thermal sensors.
Why It Matters:
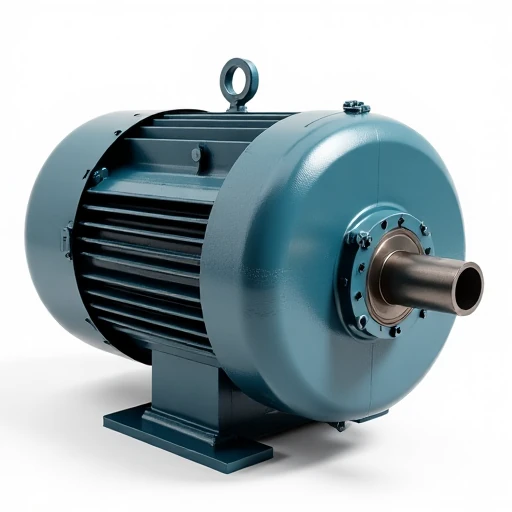
- Industry 4.0 compliance demands IoT-ready motors with predictive maintenance capabilities.
- 2025 Trend: AI-driven torque adaptation for mixed-product assembly lines.
2. Renewable Energy
Key Requirements: Weather resistance, low maintenance, high reduction ratios.
Selection Criteria:
- Motor Type: AC motors with worm gears for solar tracker systems (reduction ratios up to 300:1).
- Environmental Protection: IP68 or IP69K for offshore wind turbine pitch control.
- Material: Stainless steel gears with corrosion-resistant coatings for tidal energy systems.
Case Study: A California solar farm cut maintenance costs by 30% using self-locking worm gear motors to stabilize panels in 100 km/h winds.
Why It Matters:
- EU’s 2025 Renewable Energy Directive mandates 50-year lifespan for critical components.
- 2025 Trend: Hybrid gearboxes combining planetary and spur gears for 98% efficiency in wind turbines.
3. Logistics & Warehousing
Key Requirements: Energy efficiency, compact design, rapid start-stop cycles.
Selection Criteria:
- Motor Type: DC gear motors for AGVs (Automated Guided Vehicles) needing precise speed control (0.1–500 RPM).
- Gear Design:
- Spur Gears: Low-cost palletizers handling <500 kg loads.
- Planetary Gears: High-density AMRs (Autonomous Mobile Robots) in e-commerce warehouses.
- Smart Features: Encoders for real-time positioning accuracy (±0.5 mm).
Case Study: An Amazon fulfillment center reduced energy use by 25% using regenerative braking BLDC gear motors in 10,000+ AGVs.
Why It Matters:
- Global warehouse automation market to hit $41 billion by 2027 (Statista, 2025), driving demand for modular motors.
4. Healthcare & Medical Devices
Key Requirements: Sterility, silence, and electromagnetic compatibility (EMC).
Selection Criteria:
- Motor Type: Micro BLDC motors with harmonic drives for surgical robots (torque ripple <2%).
- Material: Medical-grade aluminum housings and FDA-approved lubricants.
- Certifications: ISO 13485 for MRI-compatible non-magnetic gears (e.g., titanium planetary gears).
Case Study: A Boston hospital upgraded MRI table actuators with zero-backlash planetary gears, reducing scan retakes by 15%.
Why It Matters:
- Rising demand for portable medical devices requires lightweight (<5 kg) gear motors with 10,000+ hour lifespans.
5. Agriculture & Food Processing
Key Requirements: Corrosion resistance, washdown capability, variable speed.
Selection Criteria:
- Motor Type: Stainless steel helical gear motors for fertilizer spreaders (IP69K, 316L steel).
- Hygiene: Smooth surfaces and NSF-certified seals for meat processing conveyors.
- Power Range: 0.75–15 kW motors for grain silo augers handling 50-ton/hour loads.
Case Study: A Dutch dairy plant eliminated bacterial contamination by switching to fully enclosed, oil-free gear motors.
Why It Matters:
- Farm-to-fork traceability laws (e.g., EU 2025 Food Safety Act) require motors with embedded RFID tags for maintenance tracking.
6. Automotive & EV Manufacturing
Key Requirements: High torque-to-weight ratios, thermal stability, and rapid prototyping.
Selection Criteria:
- Motor Type: Planetary gear motors for EV battery assembly robots (peak torque 500 Nm).
- Cooling: Liquid-cooled housings for paint shop conveyors operating at 60°C+.
- Customization: Modular designs allowing quick gear ratio swaps for hybrid/electric powertrain testing.
Case Study: A Tesla supplier reduced EV drivetrain testing time by 20% using AI-optimized gear motors with digital twins.
Why It Matters:
- EV gearbox market to grow at 14.5% CAGR through 2030 (MarketsandMarkets, 2025), demanding motors compatible with 800V battery systems.
7. Mining & Heavy Machinery
Key Requirements: Extreme durability, shock resistance, and overload protection.
Selection Criteria:
- Motor Type: Hydraulic motors with hardened helical gears for rock crushers (HRC 60+).
- Protection: Explosion-proof (ATEX) certifications for coal mine ventilators.
- Reduction Ratio: 50:1 to 100:1 for conveyor belts moving 2,000+ tons/hour.
Case Study: A Chilean copper mine extended gear motor lifespan by 3x using diamond-like carbon (DLC) coatings on gear teeth.
Why It Matters:
- Mining automation investments will exceed $15 billion by 2026 (GlobalData, 2025), requiring motors with 10-year+ service intervals.
8. Aerospace & Defense
Key Requirements: Lightweight construction, extreme temperature resilience, and MIL-SPEC compliance.
Selection Criteria:
- Motor Type: Titanium planetary gear motors for drone actuators (weight <2 kg, torque 50 Nm).
- Temperature Range: -55°C to 200°C operation for satellite deployment mechanisms.
- Precision: Aerospace-grade bearings with <0.5 arcmin backlash for missile guidance systems.
Case Study: Lockheed Martin reduced UAV actuator weight by 40% using 3D-printed Inconel gears.
Why It Matters:
- Next-gen hypersonic vehicles require gear motors surviving Mach 5+ speeds and 1,000°C+ temperatures.
Cross-Industry Supplier Selection Checklist
- Certifications: ISO 9001, CE, UL, and industry-specific standards (e.g., ATEX, FDA).
- Testing Capabilities: Request third-party reports on efficiency (IEC 60034-30), gear durability (ISO 6336), and EMC.
- Customization: Ensure suppliers offer CAD-supported design for non-standard shafts or flanges.
- Sustainability: Opt for RoHS-compliant motors with recyclable materials to meet 2025 EU carbon tariffs.
- After-Sales Support: Prioritize vendors with 24/7 multilingual tech support and global spare parts hubs.
Conclusion
Selecting a geared motor in 2025 is a strategic decision that hinges on aligning technical specifications with industry-specific operational, regulatory, and sustainability goals. By partnering with a supplier that combines engineering expertise with global compliance mastery, businesses can future-proof their operations against evolving market demands.