Explore the critical role of geared motors (reduction motors) in 2025’s industrial landscape. Learn about types, benefits, industry-specific uses, and how to choose a reliable global supplier.Keywords: Geared motor, reduction motor, industrial gear motors, high-torque motors, geared motor applications, global motor suppliers.
Introduction
In an era of automation and energy transition, geared motors (reduction motors) have become indispensable for industries seeking precision, power density, and sustainability. From robotic assembly lines to wind turbines, these systems combine motors and gearboxes to deliver optimized torque and speed control. With the global geared motors market projected to reach $32.8 billion by 2027 (Allied Market Research, 2025), businesses must understand their strategic value in reducing operational costs and carbon footprints.
As a 25+ year veteran in industrial motor exports, we specialize in providing ISO-certified geared solutions tailored to global markets. This 4,000-word guide offers a deep dive into geared motor technology, emerging trends, and actionable insights for engineers, procurement managers, and sustainability officers aiming to future-proof their operations.
1. What Is a Geared Motor?
A geared motor (or reduction motor) integrates an electric motor with a gearbox to reduce output speed while increasing torque. This mechanical advantage makes it ideal for applications requiring controlled motion under heavy loads.
Key Components:
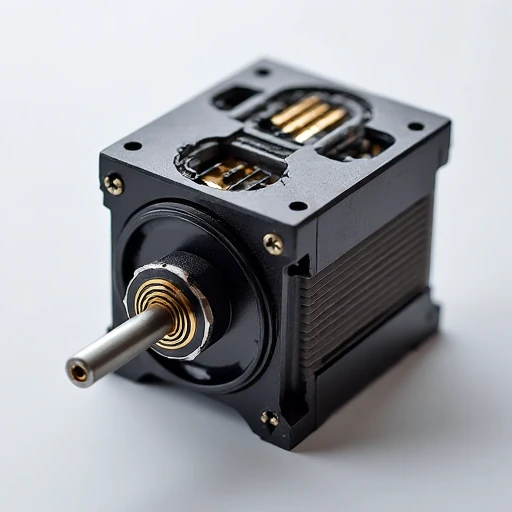
- Motor: AC/DC/BLDC types, providing initial rotational energy.
- Gearbox: Transmits power via gears (spur, helical, planetary, etc.) to modify speed-torque ratios.
- Output Shaft: Delivers adjusted motion to driven equipment.
- Housing: Protects internal components from dust, moisture, and thermal stress.
How It Works:
- The motor generates high-speed, low-torque rotation.
- Gears mesh to reduce speed proportionally (e.g., 10:1 ratio = 10x torque increase).
- The output shaft delivers optimized power for industrial processes.
2. Types of Geared Motors and Their Industrial Applications
2.1 By Gear Design
- Spur Gear Motors:
- Features: Simple, cost-effective, 95–97% efficiency.
- Applications: Conveyors, packaging machines, low-noise environments.
- Helical Gear Motors:
- Features: Angled teeth for smoother engagement, 98% efficiency, handles higher loads.
- Applications: Cement mixers, mining equipment, heavy-duty extruders.
- Planetary Gear Motors:
- Features: Compact, 3–5% higher torque density than parallel shafts, 94–97% efficiency.
- Applications: Robotics, aerospace actuators, EV powertrains.
- Worm Gear Motors:
- Features: Self-locking, high reduction ratios (up to 300:1), 80–90% efficiency.
- Applications: Elevators, gate automation, solar trackers.
2.2 By Motor Type
- AC Geared Motors:
- Advantages: Robust, low maintenance, ideal for fixed-speed applications.
- Use Cases: Pumps, fans, HVAC systems.
- DC Geared Motors:
- Advantages: Precise speed control, portable power solutions.
- Use Cases: Medical devices, AGVs (Automated Guided Vehicles).
- BLDC Geared Motors:
- Advantages: Energy-efficient (IE5+), silent operation, long lifespan.
- Use Cases: Industrial robots, drones, renewable energy systems.
3. Advantages of Modern Geared Motors in 2025
3.1 Energy Efficiency and Cost Savings
- IE5 SynRM+ Gearboxes: Achieve 96% system efficiency, cutting energy bills by 25% versus IE3 models.
- Smart Load Adaptation: AI-driven controllers adjust gear ratios in real-time to match demand, reducing idle losses.
3.2 Durability in Harsh Environments
- IP69K Protection: Resists high-pressure water jets and corrosive chemicals in food processing or offshore rigs.
- -40°C to 150°C Operation: Special lubricants and materials for Arctic logistics or steel mills.
3.3 Precision Engineering
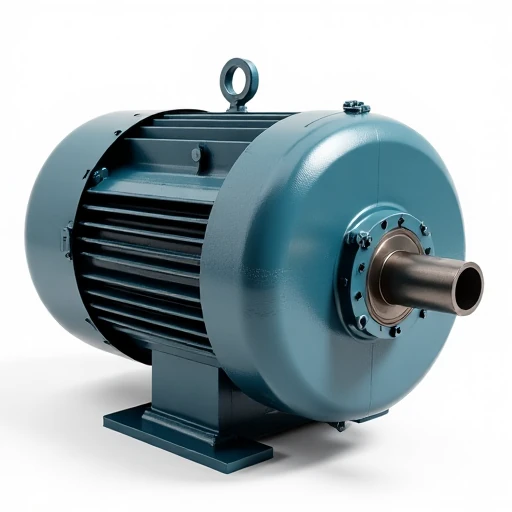
- Backlash <1 Arcmin: Critical for CNC machining and semiconductor wafer handling.
- Integrated Encoders: Provide 0.01° positioning accuracy for robotic arms.
3.4 Sustainability Compliance
- EU Ecodesign 2025: Meet strict efficiency tiers (IE5/IE6) to avoid penalties in European markets.
- Recyclable Aluminum Housings: Reduce lifecycle carbon footprint by 40%.
3.5 Modularity and Customization
- Plug-and-Play Upgrades: Swap gear ratios or motors without redesigning entire systems.
- Tailored Mounting Options: flange, foot, or shaft-mounted configurations for retrofitting legacy machinery.
4. Industry-Specific Applications of Geared Motors
4.1 Manufacturing and Automation
- Robotic Welding Arms: Planetary gears deliver high torque for precise joint assembly in automotive plants.
- 3D Printers: Stepper motor-gearbox combos enable micron-level layer resolution.
4.2 Renewable Energy
- Wind Turbine Pitch Control: Worm gears adjust blade angles during storms, ensuring grid stability.
- Solar Panel Cleaning Robots: IP67-rated motors operate in desert dust and humidity.
4.3 Agriculture and Food Processing
- Harvesting Machinery: Stainless steel helical gears withstand fertilizer corrosion.
- Conveyor Belts: Variable speed control optimizes packaging line throughput.
4.4 Logistics and Warehousing
- Autonomous Mobile Robots (AMRs): Compact DC gear motors navigate tight aisles in Amazon-style fulfillment centers.
- Palletizers: High-torque motors stack 2-ton loads with millimeter precision.
4.5 Healthcare
- MRI Table Actuators: Non-magnetic planetary gears ensure patient safety during scans.
- Prosthetic Limbs: Micro-geared BLDC motors replicate natural joint movements.
5. How to Select the Right Geared Motor: A 5-Step Framework
Step 1: Define Operational Parameters
- Load Profile: Continuous vs. intermittent duty (S1/S3 ratings).
- Torque (Nm): Calculate using T=9550×PnT=n9550×P, where PP = power (kW), nn = speed (RPM).
- Speed Range: 0.1–500 RPM common for mixers, centrifuges.
Step 2: Environmental and Regulatory Needs
- Certifications: ATEX for explosive atmospheres, FDA for food contact.
- Noise Levels: <60 dB(A) for hospital or office settings.
Step 3: Evaluate Total Cost of Ownership (TCO)
- Initial Cost: Compare planetary (higher) vs. spur (lower) gear pricing.
- Maintenance: Sealed-for-life gearboxes reduce lubrication costs by 90%.
Step 4: Supplier Capabilities
- Customization: Look for in-house R&D teams for bespoke shaft/keyway designs.
- Testing Standards: ISO 6336 for gear durability, IEC 60034 for motor efficiency.
Step 5: Future-Proofing
- IoT Readiness: Built-in sensors for Industry 4.0 integration.
- Scalability: Modular designs to accommodate future capacity expansions.
6. Maintenance and Troubleshooting Guide
6.1 Best Practices
- Monthly: Check oil levels, vibration patterns, and thermal imaging for hotspots.
- Annual: Replace seals, test backlash, and update control firmware.
6.2 Common Failures and Solutions
- Gear Pitting: Caused by overloading; upgrade to hardened steel gears (HRC 60+).
- Bearing Wear: Install condition monitoring sensors to predict failures.
- Oil Leaks: Switch to synthetic lubricants with wider temperature tolerance.
6.3 Retrofitting Legacy Systems
- Replace outdated worm gears with helical-planetary hybrids to boost efficiency by 20%.
- Add VFDs (Variable Frequency Drives) to AC geared motors for dynamic speed control.
7. Future Trends in Geared Motor Technology (2025–2030)
7.1 AI-Optimized Gearboxes
- Machine learning algorithms predict wear patterns, adjusting lubrication schedules autonomously.
7.2 Additive Manufacturing
- 3D-printed titanium gears reduce weight by 50% while maintaining strength.
7.3 Green Lubricants
- Bio-based oils degrade harmlessly in soil, slashing environmental risks.
7.4 Wireless Power Transfer
- Eliminate cabling in rotating assemblies via inductive coupling for maintenance-free operation.
7.5 Digital Twins
- Virtual replicas simulate motor performance under extreme conditions, reducing prototyping costs.
8. Why Partner with Us?
As a global leader in motor exports, we deliver:
- End-to-End Solutions: From CAD modeling to onsite installation.
- Certification Mastery: CE, UL, CCC, and GOST-R approvals for seamless market entry.
- 24/7 Global Support: Multilingual engineers in 15 time zones.
- Sustainable Innovation: Motors compliant with EU 2025 Ecodesign and REACH.
- Agile Logistics: Door-to-door delivery in 7–14 days via air, sea, or rail.
Conclusion
Geared motors are the linchpin of industrial efficiency in 2025, enabling smarter, greener, and more profitable operations. By aligning with a certified supplier equipped for tomorrow’s challenges, businesses can unlock new levels of performance and sustainability.